Mosquito Magnum+®: Get Results, Faster
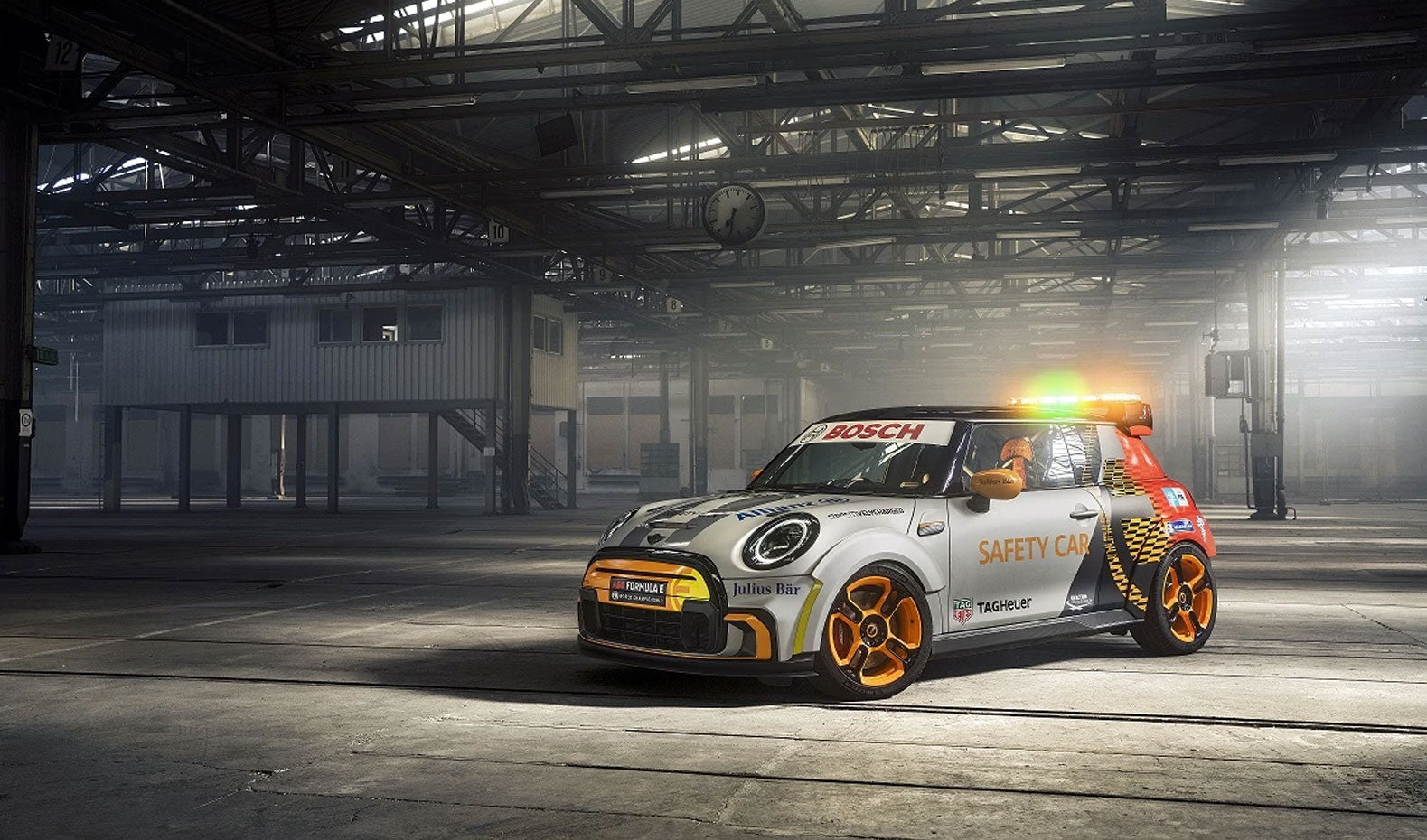
Supply chain efficiency is one of the primary concerns for most businesses. This is especially true in light of the ongoing trade wars and health crises worldwide. Manufacturers must respond to market pressures and shifting demand with great speed to stay competitive. Rapid prototyping, meeting changing demand levels, reducing operating costs, improving customer satisfaction, and room for innovation are made possible with speed.
Operations large and small are realizing 3D printing is the key to speedily improving their processes. However, a large print could take 48 hours or more for a 3D printer to complete, assuming that the print is completed correctly the first time, and no post processing work is required.
Well, you can call us Speedy Gonzales, or Superman, or Flash… or opt for the superhero cape you wore as a kid, because the Mosquito Magnum+® is the speed solution 3D printing operations are missing. Keep reading to find out why that is the case..
(Not so) Humble Beginnings
The original Mosquito® hotend was the solution to our co-founder’s mutual frustrations and conversations at work about a printing problem. From there, Slice Engineering revolutionized the hotend and the prevention of heat creep. Business owners and manufacturers all over the world now had a component that resulted in faster turnaround times and reliable quality. As an example, the U.S. Navy uses Slice products to print and replace parts that could normally take months. In this case, saving time means saving lives.
The Mosquito® Magnum+ had a similar beginning…
“The Magnum+ was inspired by conversations with small volume manufacturers and print farm owners that had a need for faster printing to increase their throughput. This was especially critical last year during the pandemic as people were cranking out face shields, face masks, and other fast response medical-related items.”
Daniel Barousse, CEO & Co-founder of Slice Engineering
Unique Benefits
The Magnum+ is a game-changer for anyone that wants to cut down on print times. Companies that benefit from rapid prototyping will find the hotend is crucial to designing, manufacturing, and testing within the quick time constraints of the market.
Material extrusion based 3D printing, or FDM or FFF, suffers from slow print times. This is due to flow rate capacity, or ability to melt and extrude filament fast enough, and kinematics, physical limitations of machine motion related to the mass of the print head. Previous to the Magnum+, the only solutions available traded quality for speed. The Magnum+ eliminated that trade off through design by thermal optimization, simultaneously addressing the issues of flow rate, resolution, and mass.
It’s comprised of all the benefits of the Mosquito® hotend line including Bimetallic Heat Break™ technology, a 500 °C temperature rating, the ability to print all filaments from basic PLA to medical-grade PAEK, and the rigid roll cage structure that enables our famous One-Handed Nozzle Change™.
For anyone that prints at volume, especially in situations where time is a critical element, Magnum+ is the only option on the market for reliable, high output prints without sacrificing print quality and resolution.
Upgrade Recommendations
Customers that buy the Magnum+ care about quality and reliability.
Our new industrial 50W heaters have been engineered from the ground up to increase MBTF (mean time between failures - a measure of reliability), especially in high-temperature applications. The Magnum+ can also be configured with a stainless steel nozzle insulator. This ensures nozzle temperatures remain at optimal print temperatures even when parts are inundated with copious amounts of cooling air.
Customers can configure their Magnum+ for optimal flow rates based on their needs.
Get Results
Case Study: Mini Formula-E Car
Munich, Germany - Once upon a time, MINI and John Cooper Works had a vision for the ABB FIA Formula E World Championship. MINI, a British automotive marque, set out to build a vehicle that challenged traditional design yet was fast and functional for the race track.
Using 3D printing to its advantage, the MINI Electric Pacesetter was born. The unique design of accentuated spats and increased diameter wheels give the vehicle an appearance of speed even before the electric engine takes off. These parts required extremely precise printing.
The spats and spoiler, vital to improving downforce at high speeds, were 3D printed with recycled carbon fibre using a Mosquito Magnum+. The custom full size vehicle parts were solely needed for the MINI Electric Pacesetter, so 3D printing was much more efficient and cost effective than other methods, like injection molding. The Magnum+ allowed them to print the large parts in record time and achieve deadlines for the upcoming race. The removable pads on the sport seat were also 3D printed. These can be customized to the driver’s preferred thickness, hardness, and color.
The MINI Electric Pacesetter is modified to meet the requirements of an FIA Formula E safety car, making it 130 kg lighter and achieving 181 hp of power and 280 Nm of torque. Making it significantly faster around a track than the production version of the MINI SE. The Pacesetter had its debut in Rome at the ABB FIA Formula E World Championship.
3D printing is making history allowing for both improved quality and design customization in the automotive industry. In another example, Radford, a British carmaker known for custom Bentleys, Aston Martins and Minis, is bringing back the classic Lotus Type 62-2 race car using 3D printing.
Case Study: Dustless Tools
Price, Utah - A small American manufacturer, Dustless Tools, was striving to onshore production and increase innovation. However, it had a bottleneck in production.
The team was looking to print a large tire, 18” in diameter, out of TPU. With the Mosquito® Magnum hotend, using a 1.2mm nozzle they could print at an average printing speed of 40mm/s. The part is approximately 2.4kg and had a print time of 23 hours, so they could print one in a 24 hour period. With the Magnum+ hotend using the same 1.2mm nozzle they were able to achieve a print speed of 70mm/s and gave a print time of just under 13 hours. The Magnum+ gave Dustless Tools the ability to double production output.
When printing with PETG, they had basic parts printing at 90mm/s. After upgrading, they were able to achieve up to 120mm/s. In some cases, the Magnum+ hotend allowed them to more than double production on the same 3D printer.
...pause for dramatic effect.
“Overall the Magnum+ hotend has proven to be very reliable and stable, we are still pushing the boundaries with it and can’t wait to see the results.”
Jason Marshall, Engineering Technician at Dustless Tools
Dustless tools is an industry leader in dust control systems, vacuums, universal-fit dust shrouds and attachments for dust free job sites. The Magnum+ hotend continues to be an asset to its production.
At Slice we have been praised for our attention to detail and commitment to quality. We will continue to carry those attributes to future innovations that make our world more efficient. You can learn more about the Mosquito Magnum+® here.